Anchor manufacturers publish a dizzying array of data about their fasteners’ capacity in various substrates under various conditions. It’s often the structural engineer’s task to identify the most appropriate anchor for the loading demand, the given substrate, and the physical boundary conditions.
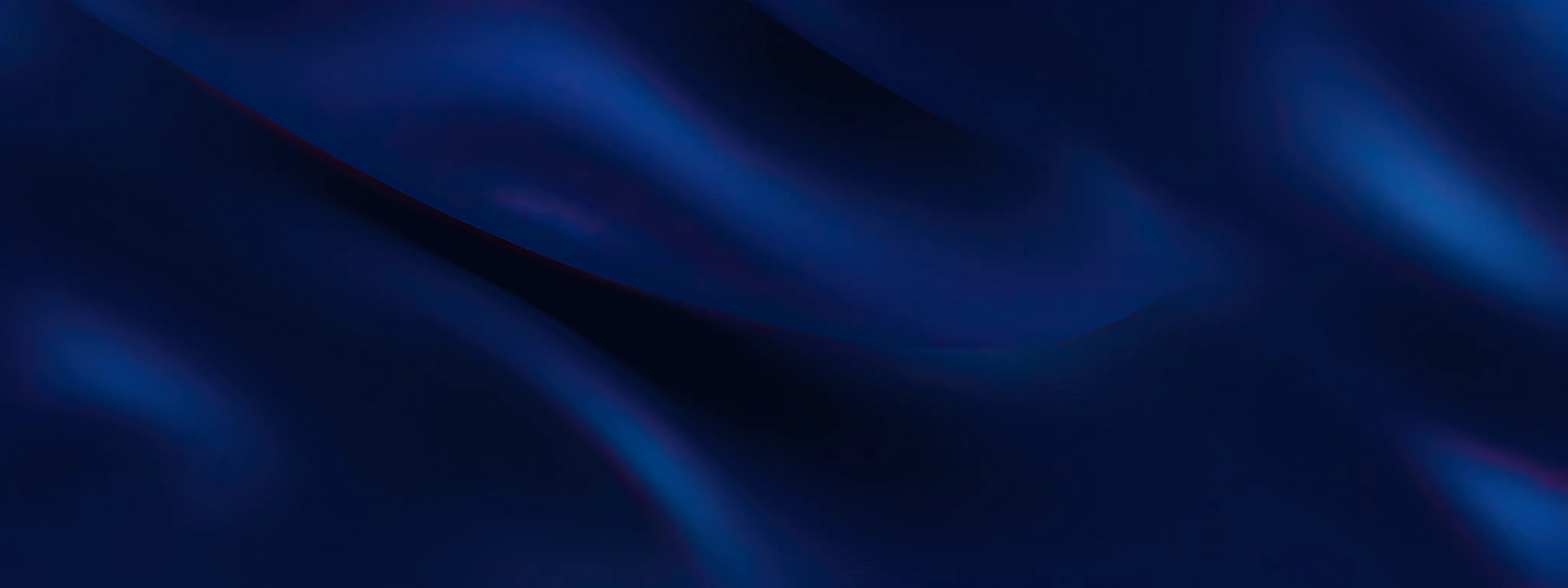
1. WHEN IT’S TIME FOR AN ANCHOR TEST
Unfortunately, not all anchor choices are so straightforward.
SOCOTEC performed a site investigation, design, construction documents, and construction administration services for the restoration of the historic art-deco downtown Boston façade of the Hudson Building located at 75 Kneeland Street. A portion of replacement precast concrete panels would be anchored back to a brick rubble infill substrate. The rubble walls occupied the spaces between the reinforced concrete columns and spandrel beams of the 14-story-high tower. However, popular anchor manufacturers that SOCOTEC usually specifies did not provide load tables for substrates consistent with what we discovered in the field. Yet the choice of anchor was not inconsequential; the fastener would be required to resist significant pullout forces to support the relieving angles carrying the heavy precast concrete panels.
SOCOTEC and the owner agreed that field testing of anchor options was necessary.
2. INTERPRETING THE TESTING RESULTS
SOCOTEC chose two regularly available epoxy anchors, and hired an outside testing firm to perform pull-tests on epoxy threaded rods in the rubble substrate. The test was performed on four (4) pairs of two (2) anchor types – here called anchors #1 and #2.
The following table gives the testing procedure:
Table 1: Anchor pull test profile

The calibrated results from the testing firm were as follows:
Table 2: Anchor pull test results (pullout loads to failure)

There was an oversight in the testing procedure, however: In each test pair, the #1 and #2-type anchors were installed within blowout distance of each other. In the first three (3) of four (4) tests, the #1 anchor was tested to failure first testing the #2 anchor (so the concern is that the substrate may have failed before testing anchor type #2, in other words). SOCOTEC suspected that these conditions explain the two (2) relatively low #2-type anchor capacity results shown in Table 2 when compared with the #1 counterparts. Consequently, SOCOTEC advised the owner that the ultimate pullout capacity of the #2-type anchor in the rubble infill substrate was 2,700 lb in the mortar joint and 3,200 lb in the brick face.
Except for the 1,450 lb capacity result, the #1 anchor results are generally consistent. This anomalous, low magnitude result may have been due to preexisting damage or looseness to the specific substrate brick in the first trial. Therefore, SOCOTEC advised the owner that the ultimate pullout capacity of the #1-type anchor in the rubble infill substrate was 4,500 lb in the mortar joint and 5,180 lb in the brick face.
With these results in mind, anchor locations and spacings were chosen, and the precast panels were installed. The project was completed ahead of schedule.
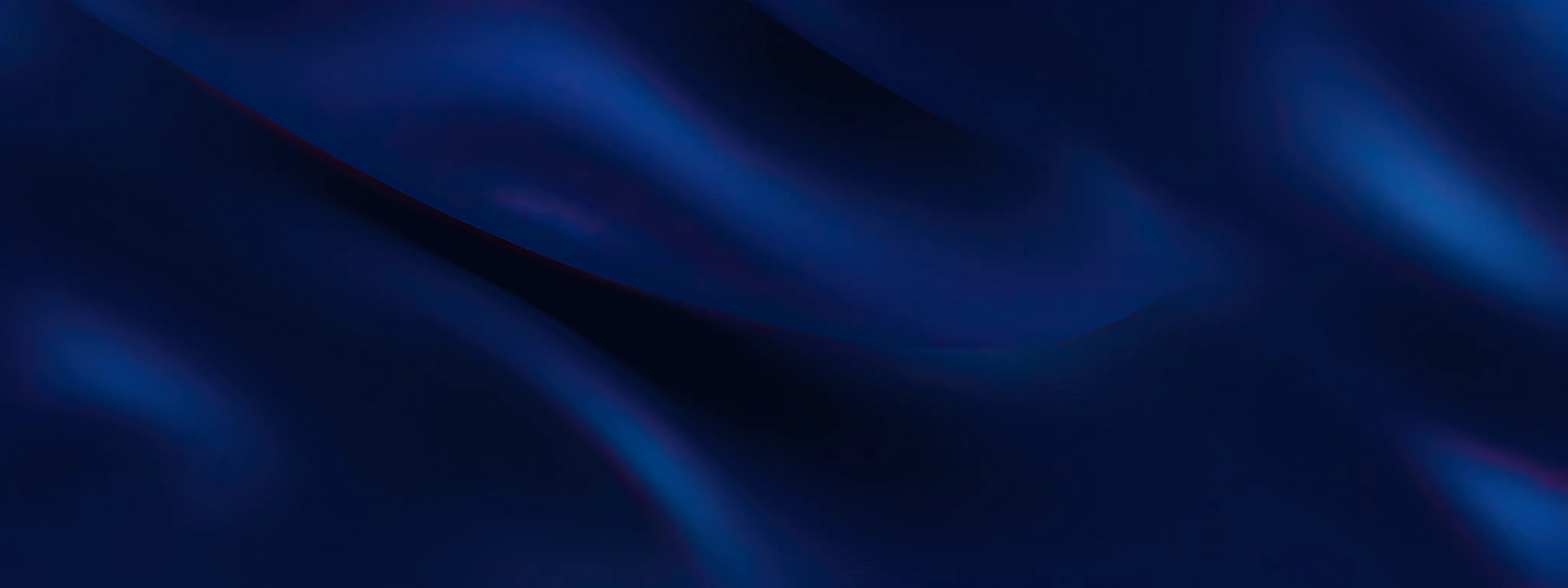
Add new comment