Cladding systems can be selected for a variety of reasons including aesthetics, costs, durability, and maintenance. When the cost of some traditional cladding systems become excessive, alternatives that are lighter weight and equal, aesthetically, can be created to save cost.
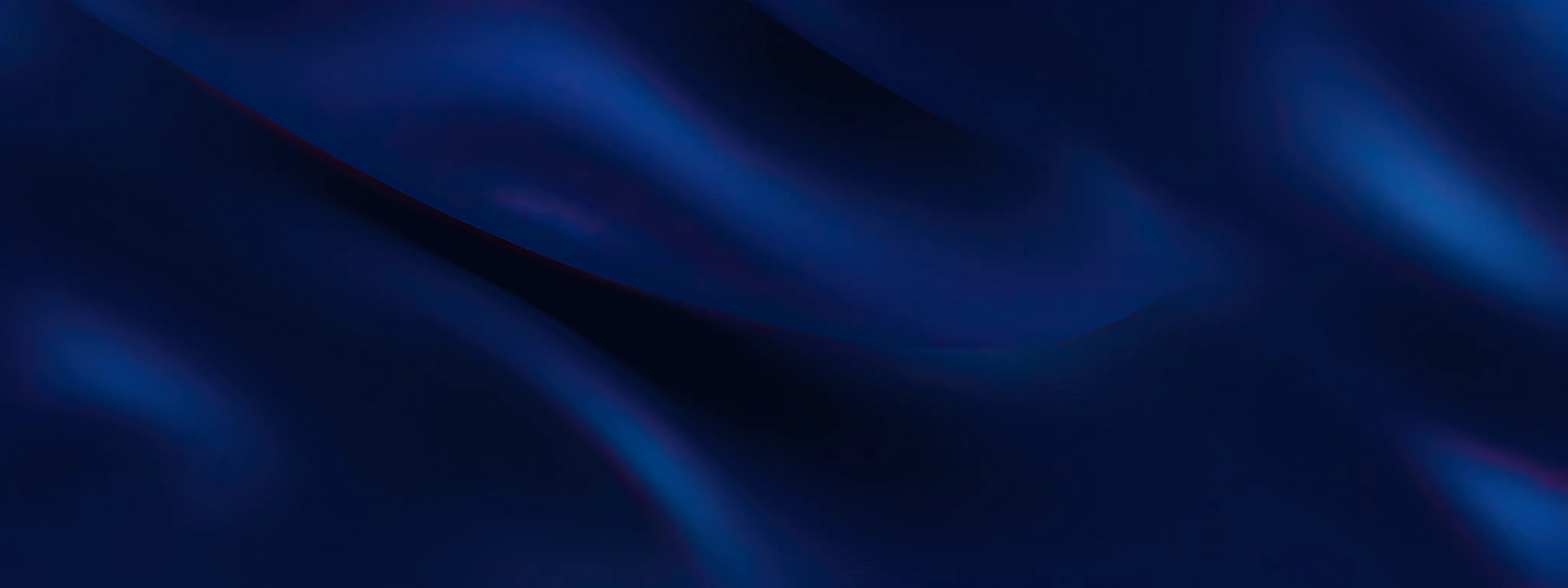
We have been successful using GFRP (glass fiber reinforced polyester) or “fiberglass” to replicate wood and terra-cotta material, for example, as alternatives to heavier and more costly traditional cladding systems. Fiberglass can be created in molds that are formed from the original material. At the Lenox Hotel, for example, we removed existing terra-cotta sills, window surrounds, cornices, pediments, and other decorative elements and assembled them in the shop as patterns to create the molds. The molds were then used to shape the fiberglass into the parts necessary to create the new skin of the building. One advantage of a GFRP assembly is that it is extremely low maintenance. The seams are finished with silicone sealant which is a 20+ year product.
The material can be colored and textured to replicate any finish, and at the Lenox we used it to replicate a tan colored terra-cotta with a speckled gelcoat finish. We have also used it to replicate wood in which case we could see the wood grain and paint strokes in the finish of the fiberglass as a result of the mold which was created from original wood material.
As with any cladding material the detailing is very important for installation and for waterproofing. Fiberglass should be fabricated with returns at all edges so that adjacent panels can be shiplapped and / or properly butted to provide a backstop for the joint sealants. A waterproof membrane should also be installed, behind, even though the GFRP is waterproof. Every cladding system needs a backup flashing arrangement. Stainless steel fasteners should be used and countersunk and finished with the same gelcoat material to fill in over each fastener. Blocking and clips should be long lasting and corrosion resistant.
We recommend consulting with a GFRP manufacturer, in advance of the project, in order to design the joints and seams from an aesthetic, installation, and waterproofing standpoint. For example, corners should be molded completely without a seam at the mitre, meaning the seams should be held back from the corner. Creating a corner condition can often be awkward and is easier to have the material wrap the corner. The corners also need to be plumb and a one-piece corner can establish the correct level lines.
When the original material is not available to create a mold or is not contiguous, a sculptor (or carpenter) is needed to create a replica of the item to be cast. Planning is required for this eventuality as it takes time to create another level of the assembly and needs to be coordinated and reviewed for approval.
GFRP is UV stable and intended for long-term exterior exposure. The gelcoat finish, again, comes in almost any color and we have seen the product replicate brick, wood, stone, antique marble, and the patina copper. Sampling is critical during this and any other process and we recommend that the design team visit the shop to view molds, as well as typical parts from each part of the casting process. Then the General Contractor should create mockups of each typical condition including waterproofing, blocking, all connections, and a final installation with sealants prior to full-scale production.
GFRP is just one product in your portfolio of available cladding materials. We often suggest that if an Owner does not have the ability to paint their exterior wood finish on a regular basis (every five years) that the material, if highly deteriorated, be replaced with a GFRP replication rather than new wood so that it does not have to be maintained in the future. While this product is not the solution to every problem, it often makes sense as a very low maintenance and creative cladding system.
By Michael S. Teller, A.I.A., NCARB, LEED AP BD+C
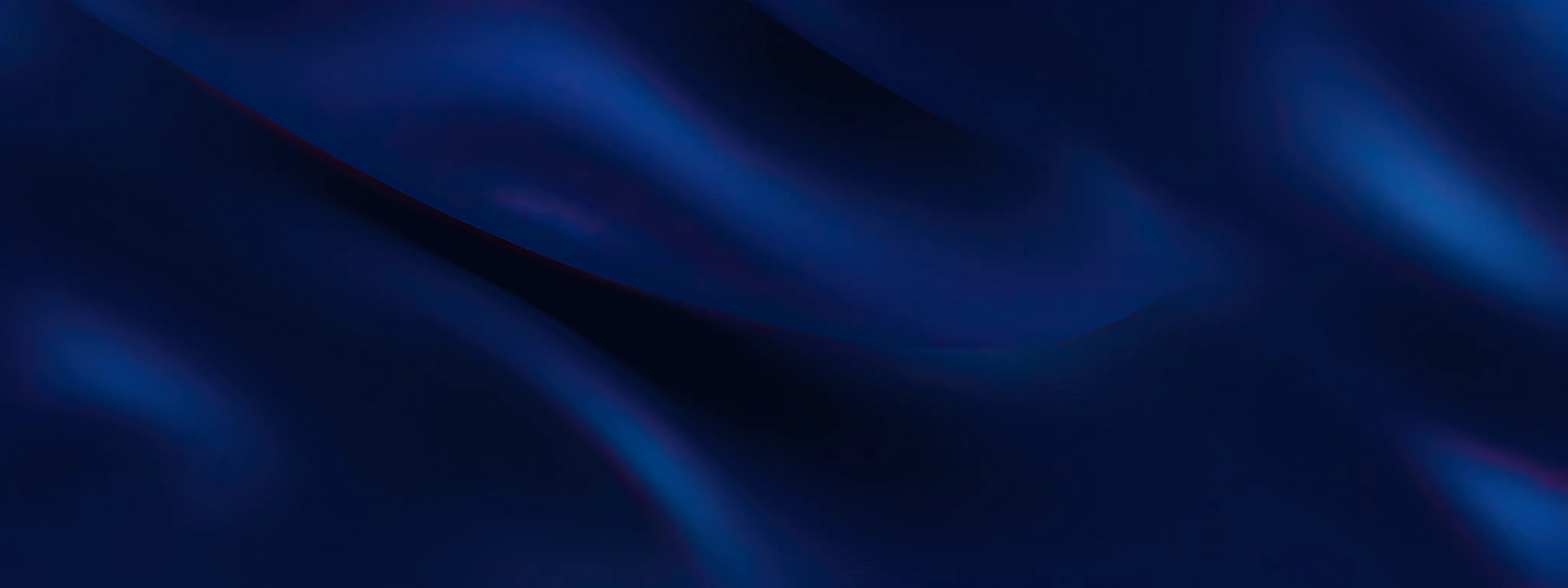
Add new comment