SOCOTEC provides mining industry services including consulting for the manufacturing of heavy equipment used in mining operations. Our services span across many verticals including heat treatment process improvement, welding repair and structural procedures, technical audits of foundries, casting and forging process evaluation, ITP evaluations and more.
Mining Industry Services
The mining industry is supported by highly specialized heavy equipment used in all phases of operation, from ore extraction through smelting and refining to final fabrication. Equipment manufacturers and vendors are constantly striving to improve their methods and processes to
Produce technically superior, reliable, cost-effective components and equipment
Eliminate costly defects and quality deviations
Minimize risk in all phases of manufacturing
SOCOTEC offers a variety of consulting and technical support services to equipment manufacturers—foundries, forges, fabricators—to meet their objectives.

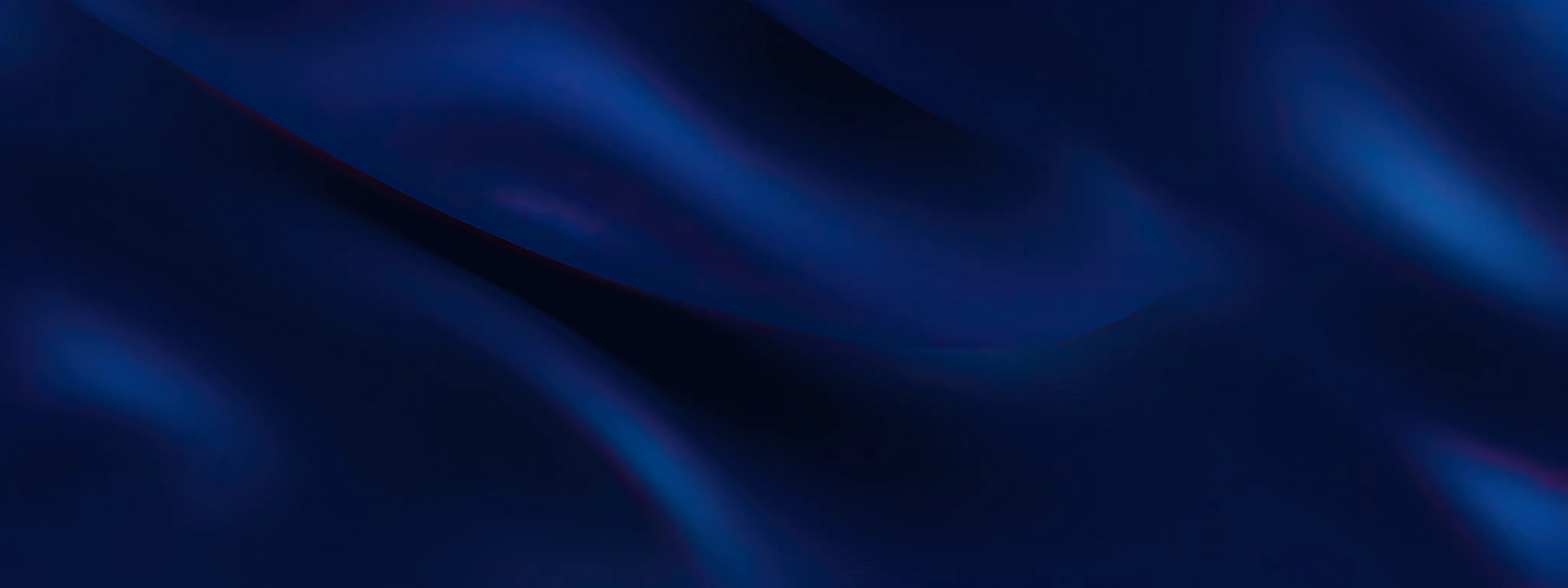
Talk to our experts
Service offerings:
Heat Treatment Process Improvement
-Optimization of cycles
-Deviations
-Reduced cycle options
Welding Repair Evaluation
-Evaluation and monitoring of welding repairs
-Structural procedure evaluation
-ASME BPVC Section IX, AWS S1.1, API RP 577 & 582, ISO Standards
Foundry Auditing
Technical audits of foundries, forges and fabrication facilities
Casting & Forging Reviews
-Casting and forging process reviews
-Solidification process reviews
-MAGMA, SOLIDCAST, etc.
ITP Evaluations
Inspection Test & Plan (ITP) evaluations outline the adequacy of a material over time through its lifecycle
Alloy Selection
Our experts will help identify the alloy best suited for your application, considering the material usage, equipment activity and life expectancy of the asset
Fitness for Service Evaluations
Failure analysis and fitness for service evaluations for castings, forgings, and fabrications
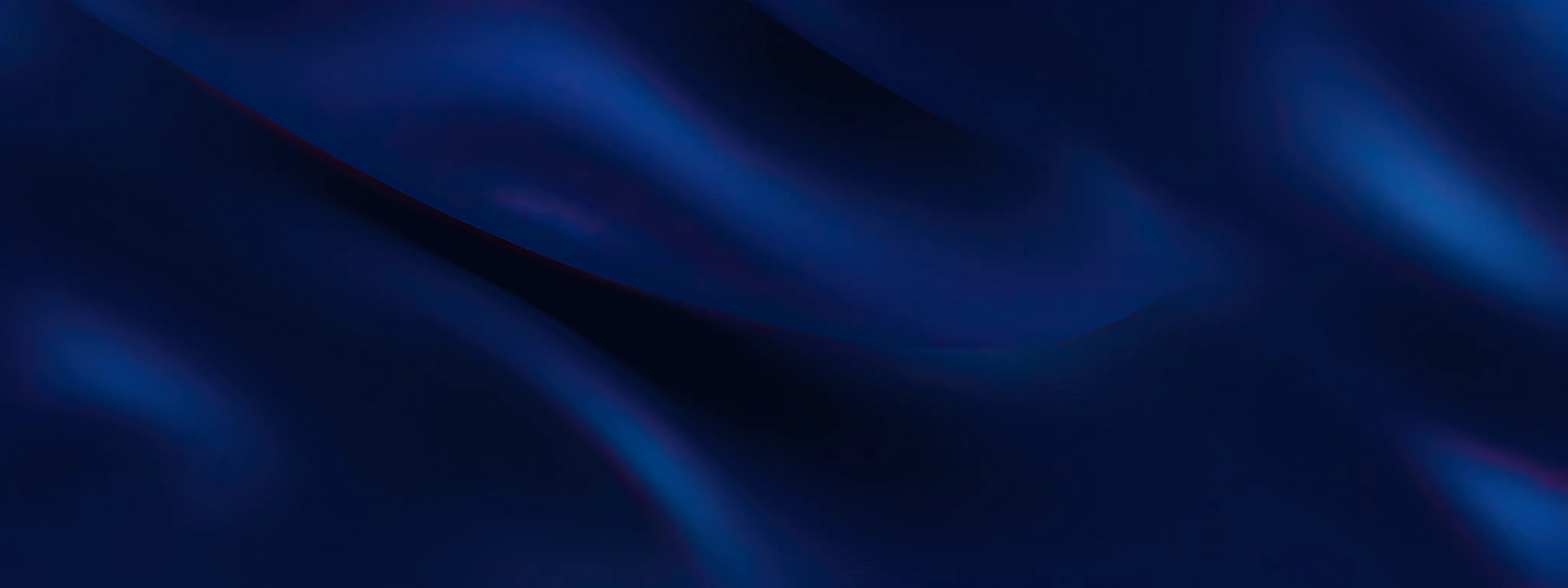
Mining Services
Project Example: Ball Mill Gear
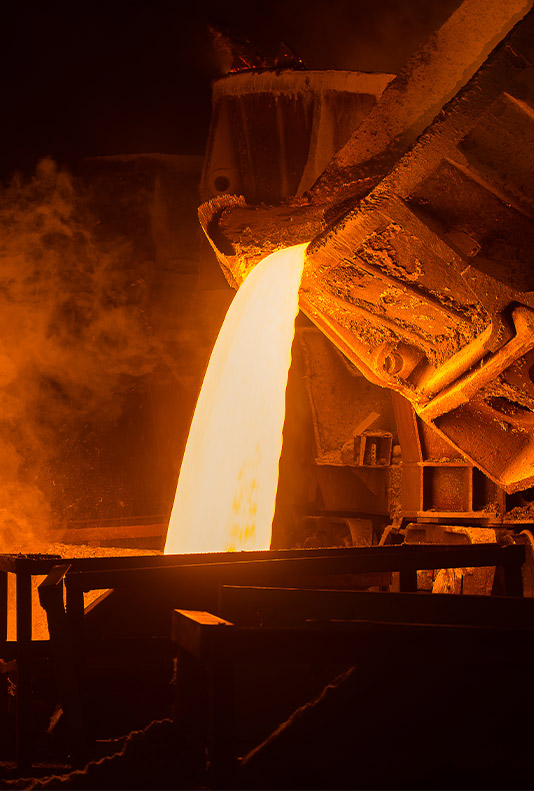
- Objective: Determine root cause of cracking
- Activities and Results
- Performed MT, visual inspection, stereo “in-situ” microscopy, chemical analysis, SEM, HB profile
- SEM determined that intergranular cracking nucleated during the solidification process
- Mode of Failure: Low cycle / High strength Fatigue.
- The crack propagated out of a casting discontinuity (gas porosity).
- Recommended Solutions
- Smooth out by grinding the affected zone and install remotely controlled strain gauges to evaluate crack propagation.
- Metal stitching the crack
- Objective: Determine root cause of cracking
- Activities and Results
- Performed MT, visual inspection, stereo “in-situ” microscopy, chemical analysis, SEM, HB profile
- SEM determined that intergranular cracking nucleated during the solidification process
- Mode of Failure: Low cycle / High strength Fatigue.
- The crack propagated out of a casting discontinuity (gas porosity).
- Recommended Solutions
- Smooth out by grinding the affected zone and install remotely controlled strain gauges to evaluate crack propagation.
- Metal stitching the crack
Want to learn more about our Mining Services?
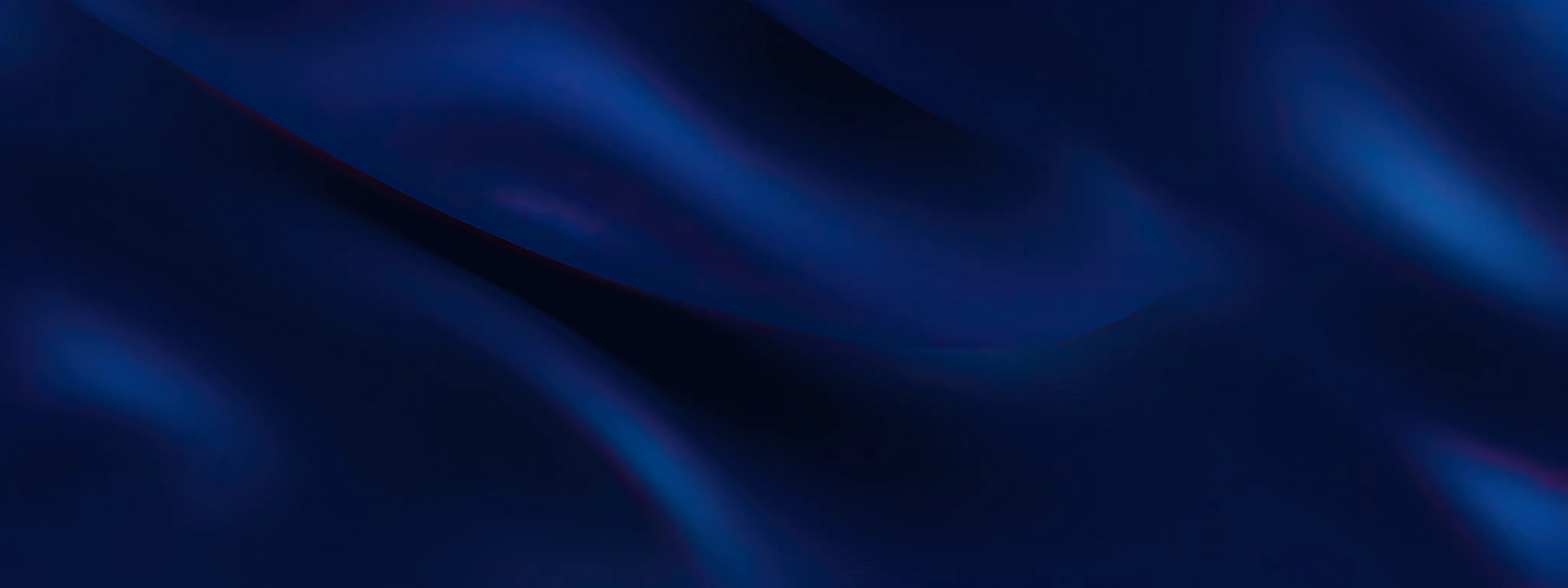