Component flaws when identified require assessment to support continued operations, and to enable the scheduling of a repair either immediately or at some future repair window, or for a nuclear plant at a refueling outage. SOCOTEC 's experts can perform such assessments to meet applicable code requirements, such as API 579/ASME FFS-1 or ASME Section XI flaw evaluations. SOCOTEC utilizes the ANSYS FEM code to perform deterministic analyses. Our capabilities extend to performing probabilistic assessments, when specific input parameters are not well defined.
Fracture Mechanics and Fatigue Analysis
SOCOTEC has the technical capabilities and professional experience to implement a full fracture mechanical and fatigue analysis for any type of structure under dynamic loading. Fracture Mechanics and Fatigue Life assessment, usually grouped under the heading of Fitness-For-Service, has always been an important consideration for the survivability of structures, and increasingly gains relevance during tight economic times as clients strive to curtail capital expenditure by determining accurate life spans of their structures.
SOCOTEC is a multidisciplinary engineering firm whose clients are drawn from across a wide spectrum of engineering, encompassing disciplines as structural, mechanical, nuclear, naval, and chemical engineering. Our Fracture Mechanics clients include transportation authorities, power utility companies, legal firms and defense contractors to name but a few.
Whether it is metallic corrosion or surface or embedded flaws in weldments or parent metal, SOCOTEC has the ability to determine modes of failure, crack initiation sites, probable rates of propagation, and remaining fatigue lives due to complex sources of dynamic loading. And most importantly, SOCOTEC has experienced staff with over a century of collective experience in the field of facture and fatigue analysis, staff that have demonstrated sound judgment and a continuing commitment to cost effect solutions.
SOCOTEC has specially trained technicians continuously deployed in the field conducting non-destructive examinations (NDE) in the determination of flaw characteristics in parental metals and weldments, as well as stress and corrosion cracks. We employ the latest technological advancements such as radiography, magnetic particle, dye penetrants, ultrasonics, and eddy currents in our work. SOCOTEC also has a fully equipped laboratory where our material behavior specialists can determine the material properties needed to perform a fracture analysis. These properties include plane strain fracture toughness, KIC, elastic/plastic fracture toughness, JIC, T, CTOD, and Charpy V-notch ductile-to-brittle behavior (-450oF to 1400oF).
SOCOTEC’s analytical capabilities center on the development of linear elastic and non-linear elastic-plastic crack growth scenarios. An integral component of this is an accurate estimation of service stress ranges, and SOCOTEC has several methods of how to achieve this. SOCOTEC can fully instrument existing structures to measure actual stress levels under operational loading. Also, SOCOTEC has a rigorous finite element analysis capability which includes the modeling of complicated connections and structural discontinuities. Both static and transient loading may be considered, in order to determine the presence of stress concentrations in the vicinity of welds and bolt holes. Thus, using these NDE techniques and linear/non-linear facture mechanics principals, SOCOTEC can determine the criticality of existing flaws and the projected life of a structure under expected loading. If significant crack growth currently exists in a structure, SOCOTEC can develop remediation strategies to stop future crack growth, thus extending the life of the structure.
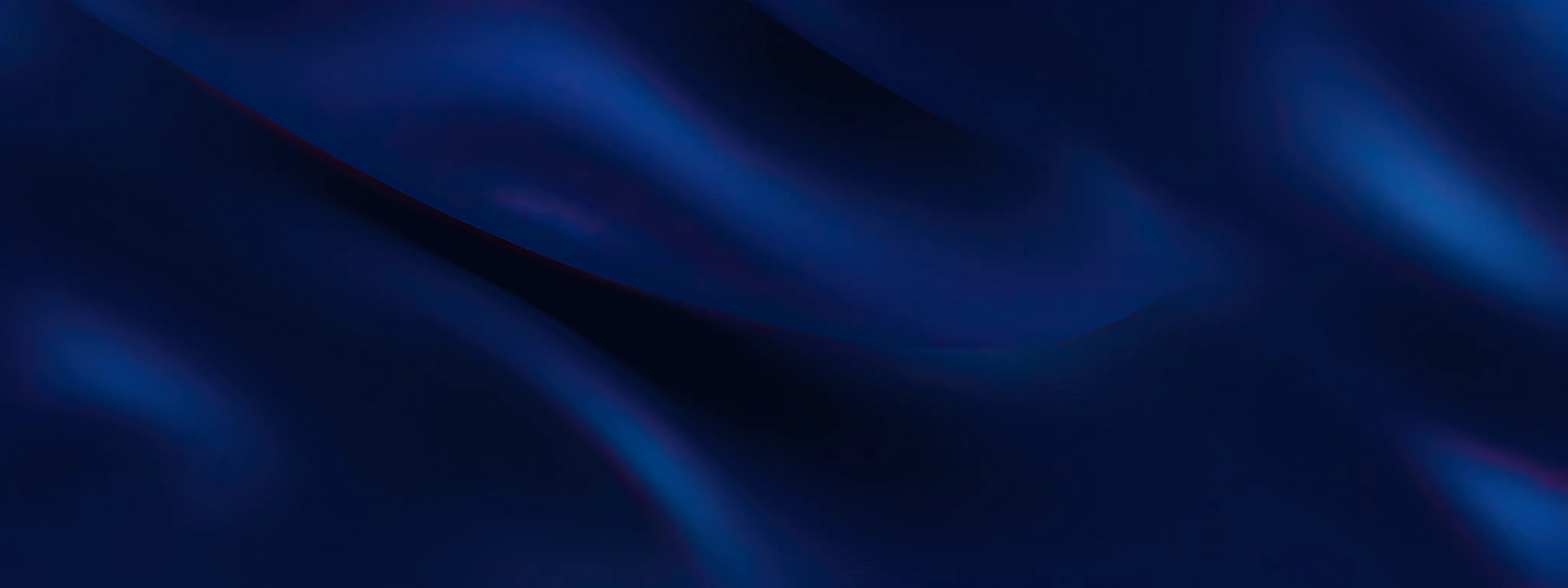
Talk to our experts
Want to know more about our fracture mechanics or fatigue analysis services?
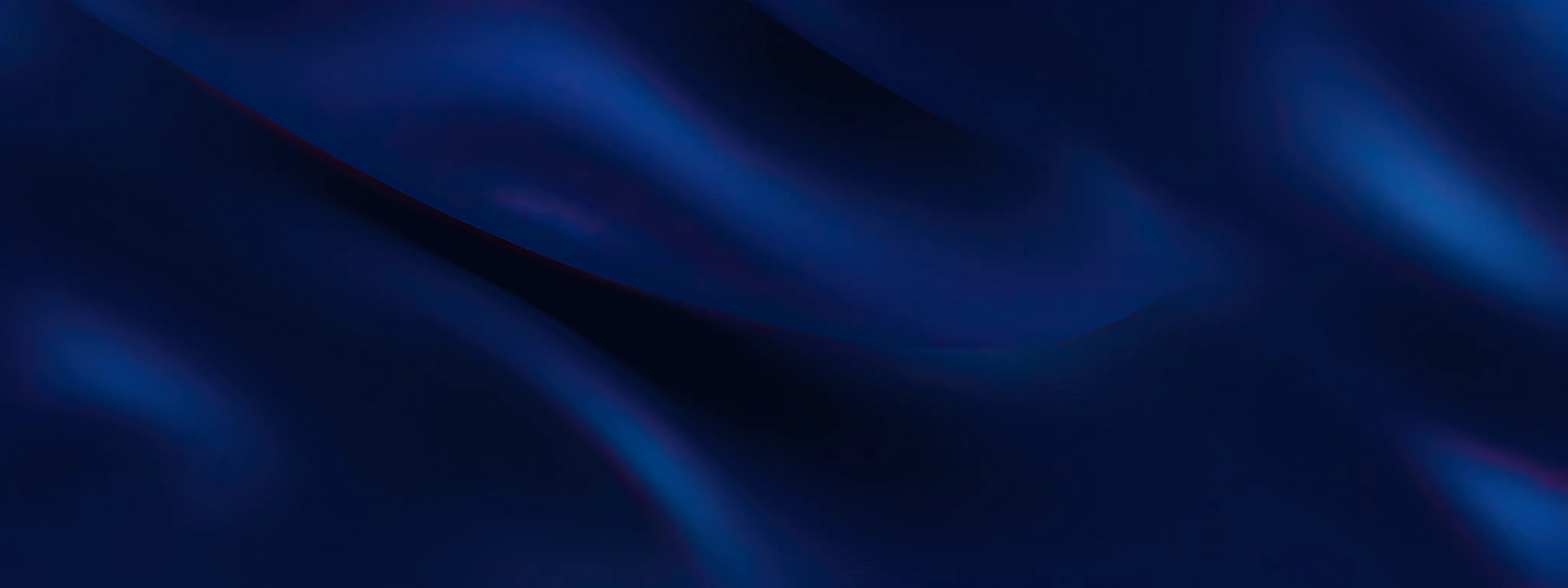